Engine Driven Chillers
I Overview
Engine-driven chillers cool water using energy provided by a natural gas engine. They operate similarly to electric chillers, substituting the electric motor for an engine to drive a compressor.
The chiller consists of four main components through which a refrigerant cycles: the compressor, condenser, expansion valve and evaporator. This internal structure is just the same as an electric chiller.
II Applications
The engine that drives the compressor in an engine-driven chiller can operate at multiple speeds, which means that one unit can handle multiple loads. This stands in contrast to electric chillers, which cannot do so without expensive variable speed motors. In fact, a gas engine driven chiller can typically run at 20% of rated capacity without losing efficiency. This means that the gas engine chiller can handle smaller cooling loads in the shoulder months, such as April, May, October and November, as efficiently as full loads in July.
Engine-driven chillers are generally used to provide larger tonnage cooling loads in areas with medium to high electric rates. In particular, they are often installed in hybrid systems with electric chillers. Such systems are optimized to provide the most economical cooling, often depending on the time of day. Engines are used during on-peak electric times and when loads are light, and electric might be used off-peak.
III Equipment Options
Engine-driven chillers can be cooled by air or by water, depending on the capacity of the unit. In addition, waste engine and exhaust heat can be recovered for domestic hot water production or other thermal energy needs.
Engine-driven chillers are sized from 25 tons to thousands of tons.
IV Resources
1. Equipment Manufacturer Database
2. Gas Air Conditioning Consortium
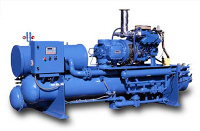