Absorption Chillers
I Overview
Absorption chillers cool water using energy provided by a heat source. They differ from conventional (vapor compression) refrigeration systems in two ways. The absorption process is thermochemical in nature, as opposed to mechanical. Also, absorption chillers circulate water as the refrigerant instead of chlorofluorocarbons or hydro chlorofluorocarbons (CFCs or HCFCs, also known as Freon).
The standard absorption chiller system uses water, as a refrigerant, and lithium bromide, as an absorbent, in its cycle. The lithium bromide has a high affinity for water. The process takes place in a vacuum, allowing the refrigerant (water) to boil at a lower temperature and pressure than it normally would, helping to transfer heat from one place to another.
Small residential-sized units use ammonia as the refrigerant, and water as the absorbent.
II Applications
In addition to being direct fired by natural gas, absorption chillers can run off of hot water, steam, or waste heat, making them an integral part of cogeneration systems or anywhere that waste heat in any form is available.
Absorption chillers are generally used where noise and vibration levels are an issue, particularly in hospitals, schools, and office buildings.
III Equipment Options
Absorption chillers can be fired directly or indirectly, and can be single-effect or double-effect. Indirect-fired chillers use heat from another source, while direct-fired chillers use a natural gas burner to power the cycle. Double effect chillers recycle some of the waste heat produced during the cycle, and thus are more efficient per unit of input heat; this efficiency comes at the cost of requiring a hotter input such as steam or natural gas.
Equipment sizes range from 4.5 tons of cooling up to several hundred tons of cooling.
IV Resources
1. Equipment Manufacturer Database
2. Gas Air Conditioning Consortium
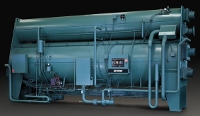